March 12, 2024
Jessica Byrd, Prime Metal Buildings
In the world of metal building manufacturing, innovation is the key to success. At Prime Metal Buildings, we understand this well. With our commitment to quality and a vision for the future, Prime has begun integrating AGT’s BeamMaster Welding Robots into their production process in 2021, propelling Prime into a new era of efficiency and precision. These robots are cutting-edge, revolutionizing the way we manufacture metal buildings. These robots, paired with our skilled employees, allow Prime to produce the same high-quality materials at an unparalleled rate.
Prime currently has four robots and will be adding four more in 2024. However, this doesn’t mean we’re planning on diminishing manpower… in fact, we are actively recruiting new team members to our growing workforce! We’re continuously hiring welders, fitters, and robot operators due to our rapidly increasing production needs. One BeamMaster consists of 2 “zones” and is run by one operator. Alone, a zone has welding capabilities of up to 40 feet. But together, both zones can complete material as long as 80 feet and up to 8,000 pounds! These robots are geared specifically for structural steel fabrication and pre-engineered metal buildings, and their Cortex structural software can process CAD plans and create a tailor-made production code for each beam in mere SECONDS!
The process is simple. The operators load the beam into the robot’s rotators, where it remains until the welding is complete and the beam is ready to be painted. This promotes efficiency on the shop floor by lessening foot traffic. The robotic rotators allow the welder to reach all angles of the beam, automatically rotating when needed. The arm takes a 3D scan, determining the welding needs for that specific location and ensuring a quick and efficient welding path, all while intricately sequencing welds to prevent heat distortion to the beam. The robots are even able to monitor their maintenance routines, which ensures that they’re producing high-quality welds, and maintaining a safe environment. Prime has seen great success with the robots and has been able to run up to 28 parts within a 10-hour shift!
The addition of robotic welders within Prime’s manufacturing process has provided many benefits for both Prime’s customers and employees, and this is only the foundation for the technological enhancements that are to come in the metal building industry.
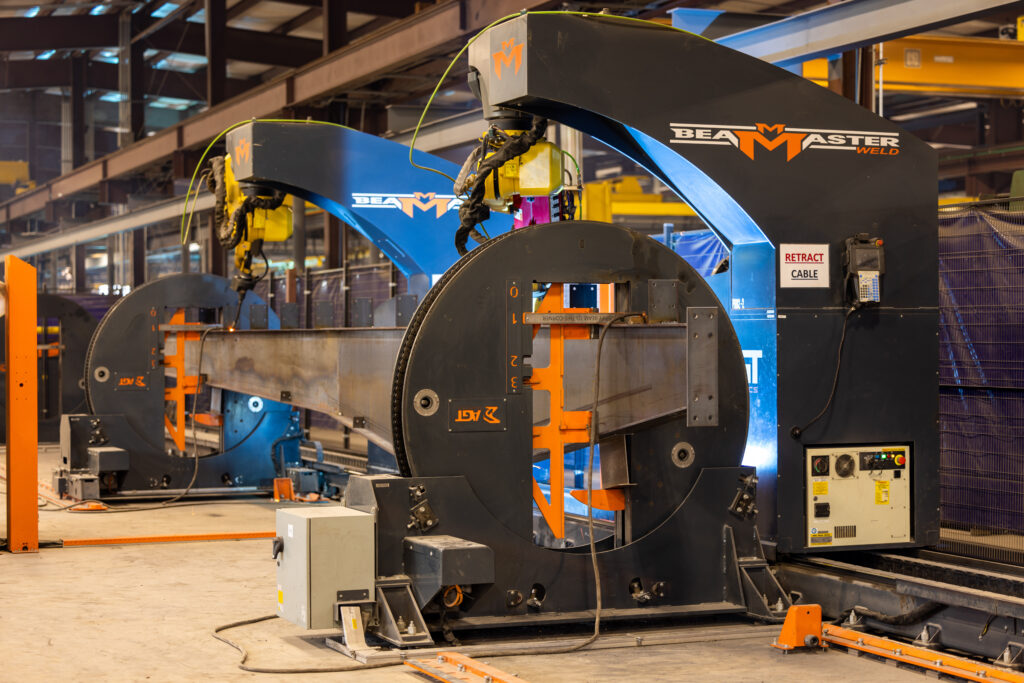
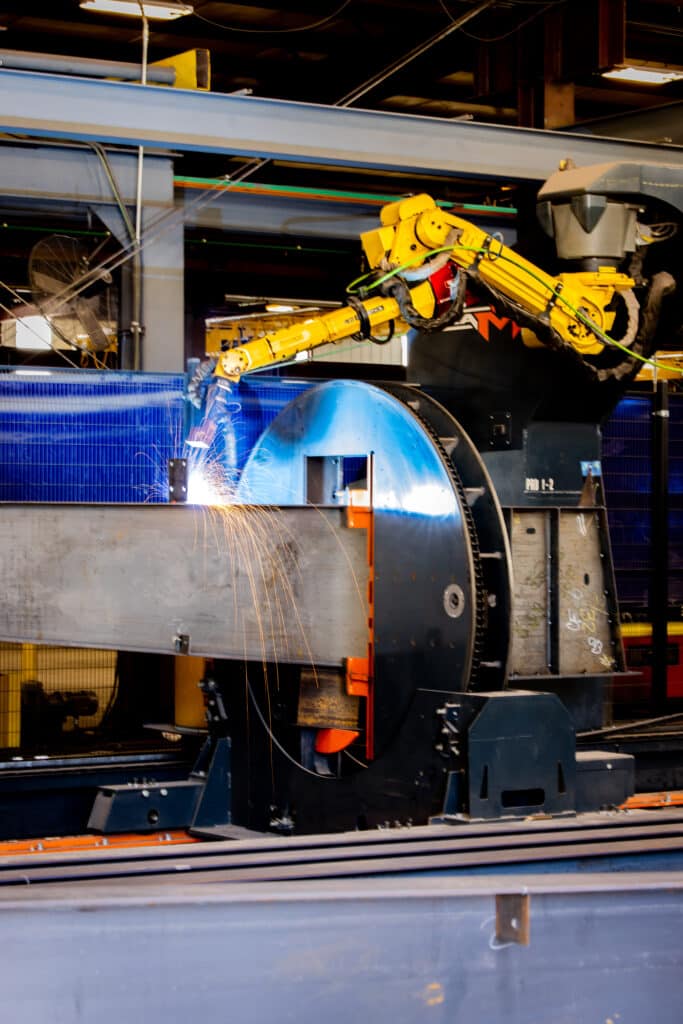
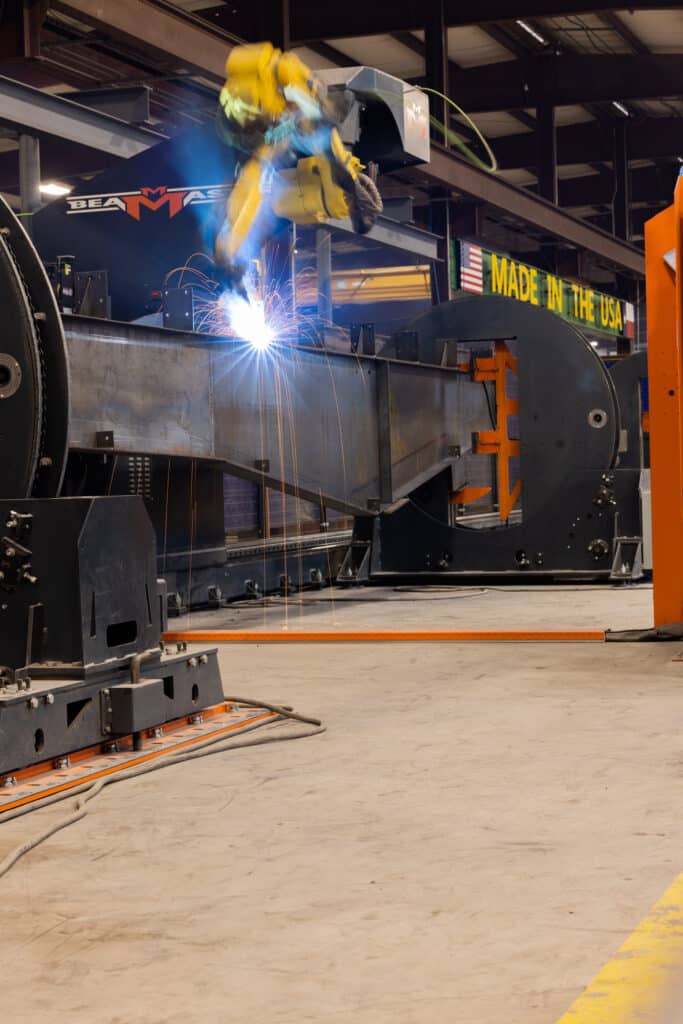
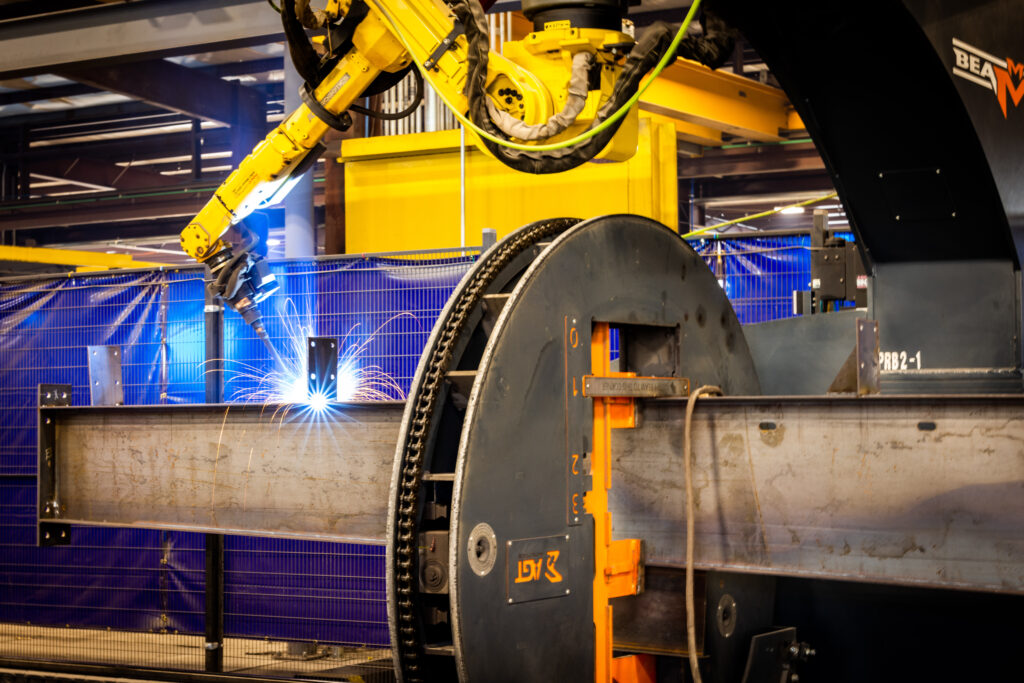